„Grieves describes the digital twin as consisting of three components: a physical product, a virtual representation of this product, and the bidirectional data links that transfer data from the physical to the virtual representation and information and processes from the virtual representation to the physical product, i.e. enable bidirectional data exchange.“
Projects
The following projects show use cases based on the Digital Miniature Factory in the subject area Digital Twins as results of scientific work of students of the UAS Technikum Wien.
Control and monitoring of a 6-axis robot
A miniaturized 6-axis robot is controlled by means of an AR application. This is made possible by a programmable logic controller (PLC) and an Industrial Internet of Things (IIoT) system. Each of the 6 axes can be selected and its angle changed. The robot performs the same movements as its digital twin.
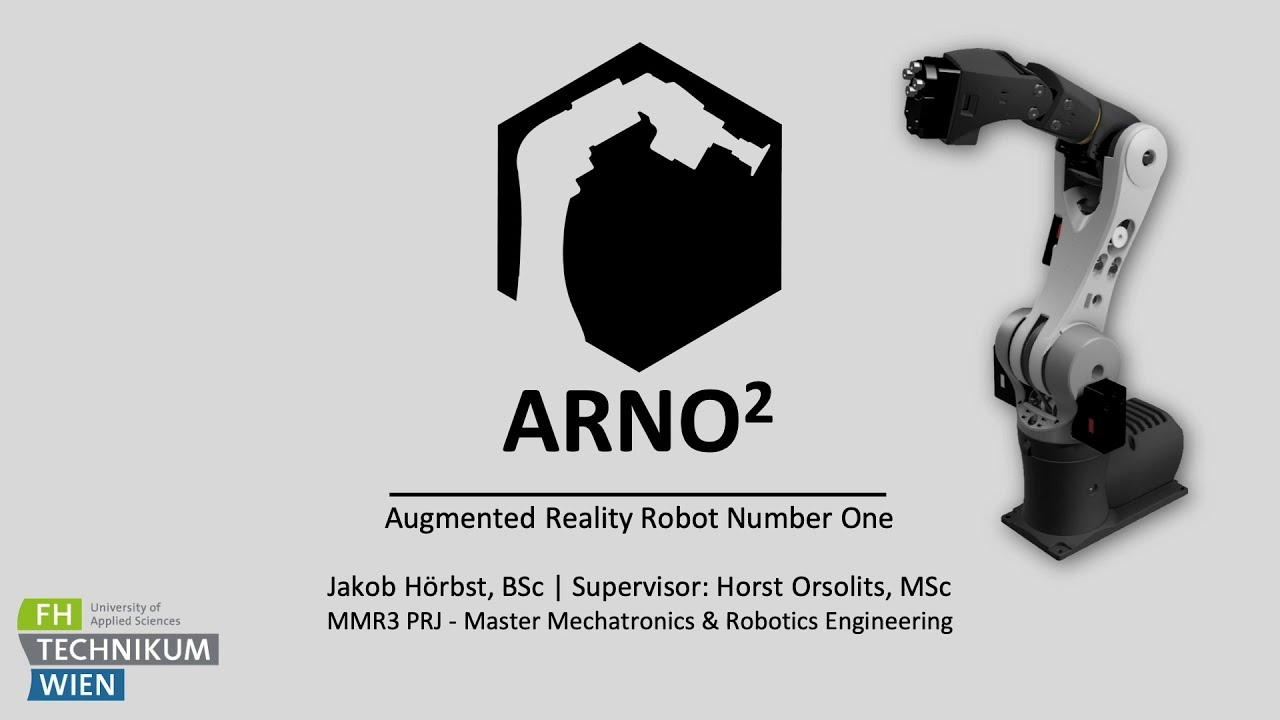
Please accept cookies for external media to view videos
Pick and place programming
By means of an AR application, a pick and place application can be realized. The user can select points in the room, which are approached by the robot. Furthermore, it must be selected at which points the robot should open and close its gripper. Thus, a pick and place application can be realized without any programming knowledge.
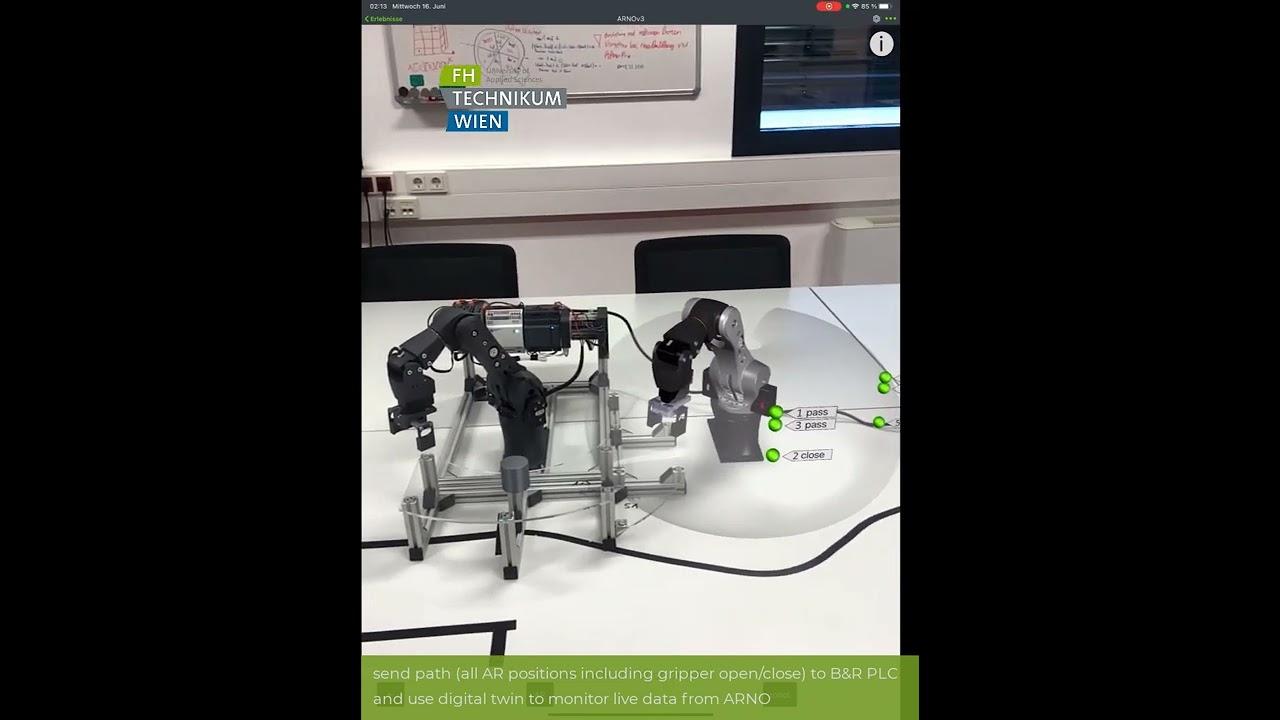
Please accept cookies for external media to view videos
Control of an industrial 6-axis robot
A virtual reality (VR) application can be used to control an industrial 6-axis robot. The physical robot is located in the Digital Factory of the UAS Technikum Wien – the digital twin of the robot is located in the digital image of the Digital Factory. In the VR environment a machining process of the robot can be started and stopped.
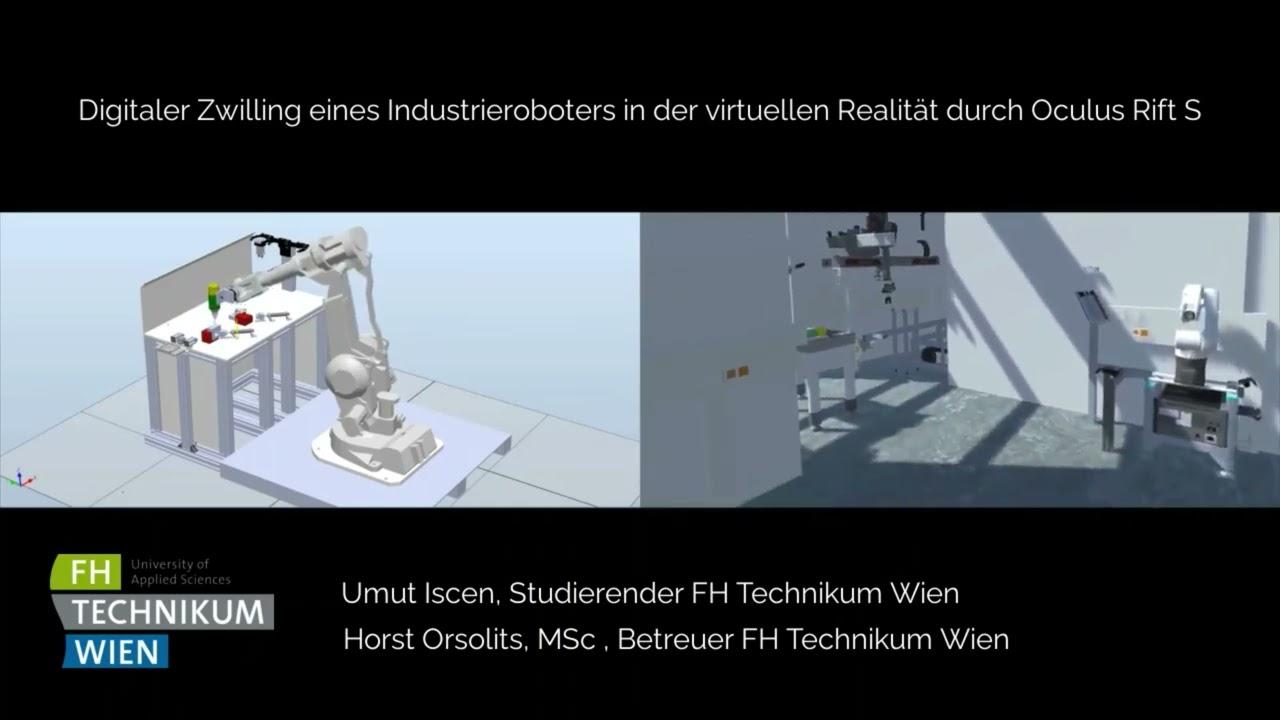
Please accept cookies for external media to view videos