Digital Miniature Factory Overview
The Digital Miniature Factory (DMF) is a smart manufacturing system in which color-customized 3D printed carabiners are picked and packed automatically. The product configuration of the carabiner is done according to individual customer requirements. The communication of the stations is based on an IIoT – platform, as well as the communication standard OPC UA. Thus, the DMF serves as a research and teaching laboratory as an ideal infrastructure for the topics of intelligent networked production, as well as digital twins in the industrial environment. Virtual commissioning also plays a central role, as do various applications of augmented and mixed reality.
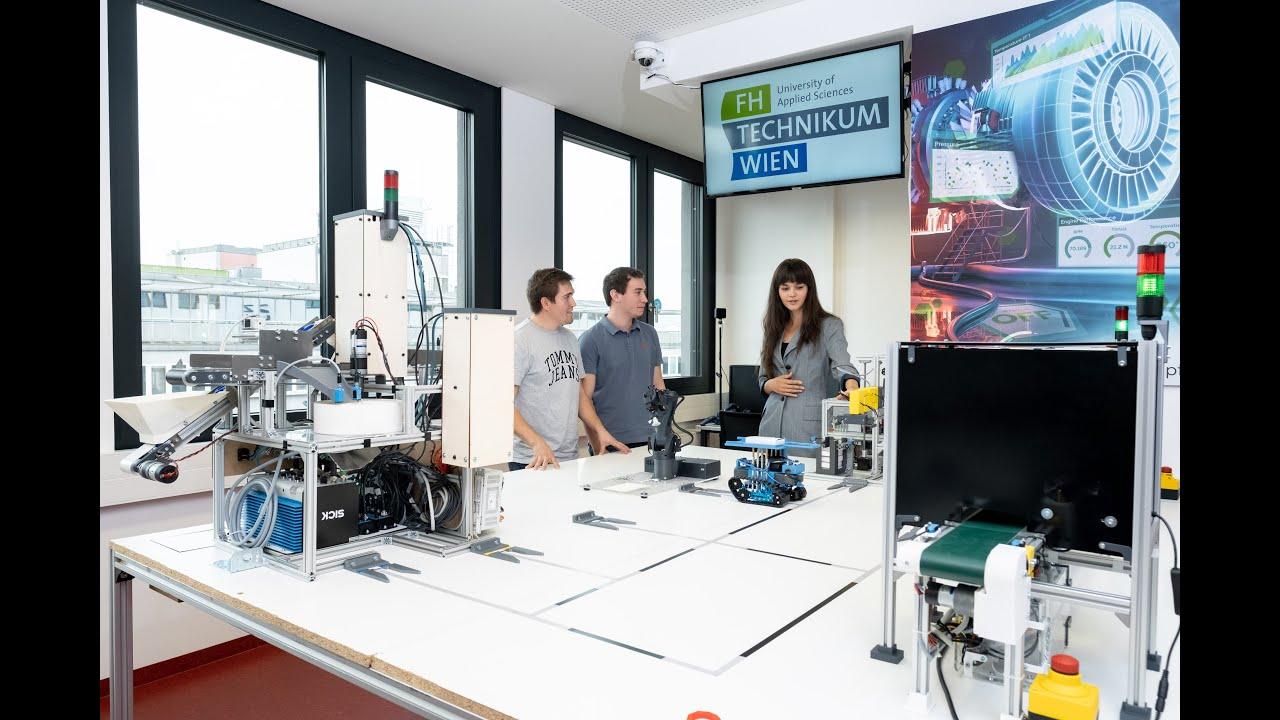
Please accept cookies for external media to view videos
Mobile robot
In the current iteration stage, the mobile robot is designed as a line follower, transporting the carabiner kit from one station to the next. By using a Dijkstra algorithm, it is ensured that the robot covers the shortest path. A mobile transport platform enables the highest possible flexibility and utilization of the production process.
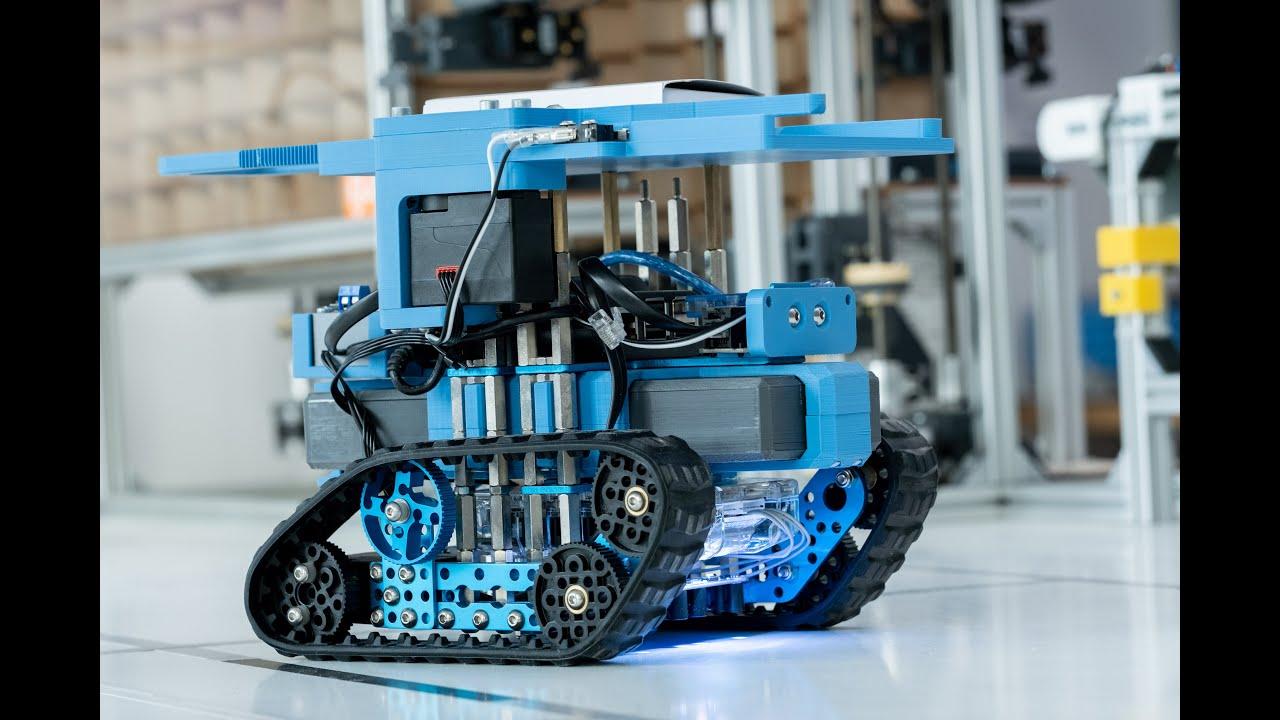
Please accept cookies for external media to view videos
Sorting station
In the sorting station, six different parts of the carabiner are separated and identified with the help of an industrial camera. The separated parts are stored in compartments of a bunker. Upon request of the mobile robot, the desired part is dispensed by the sorting station. The sorting station automatically replenishes missing bunker compartment stocks to ensure an efficient production line.
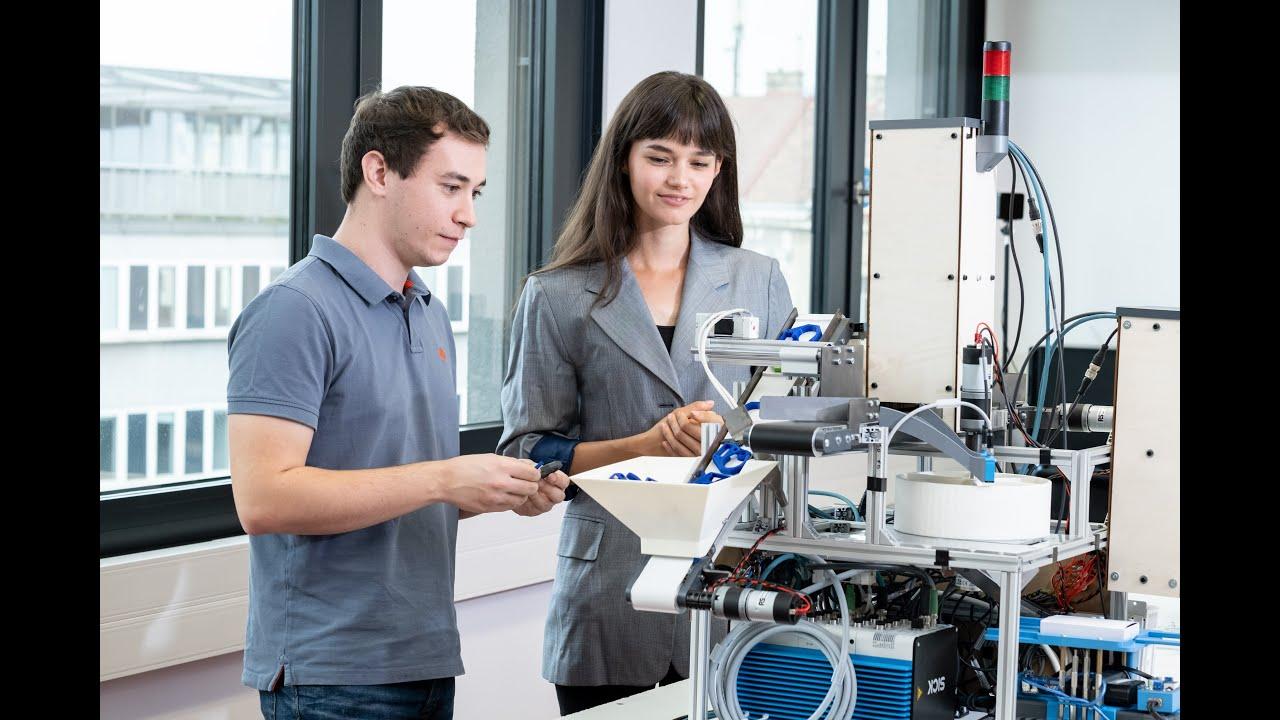
Please accept cookies for external media to view videos
Storage station
The storage station represents a miniaturized high-bay warehouse. By means of a SCARA robot, half-finished or finished products are picked up by the mobile robot and placed in an intermediate storage area. From the intermediate storage the product can be stored intelligently by means of a Cartesian carriage system. Furthermore, the product can be deposited from the intermediate storage onto a conveyor belt by means of another SCARA robot. The automated storage and retrieval of products in combination with a mobile transport platform enables the highest possible flexibility in the production process.
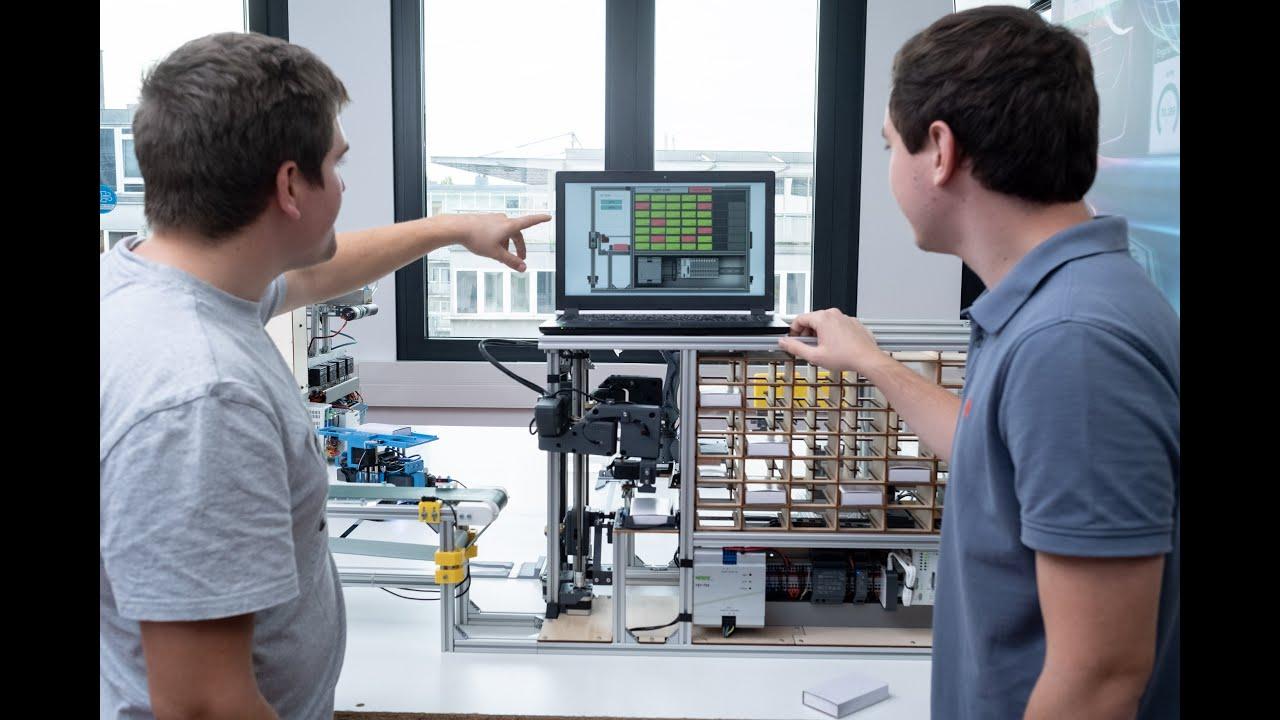
Please accept cookies for external media to view videos
Conveyor belt and engraving station
Batch size “1”, i.e. products manufactured individually according to customer requirements, is becoming increasingly important in tomorrow’s production. In the case of the Digital Miniature Factory, it is possible to freely select the color composition of the carabiner. In addition, the box of the carabiner kit can be individually engraved. The motive to be engraved can be specified via a tablet.
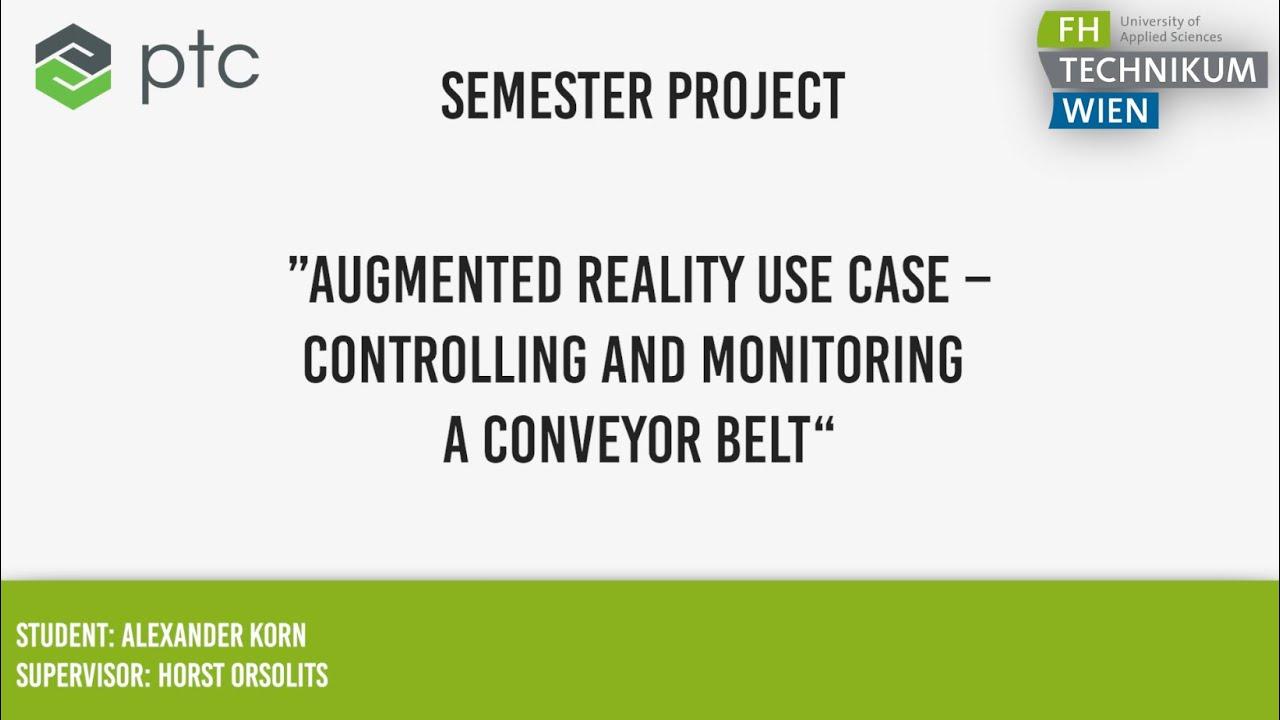
Please accept cookies for external media to view videos
Quality control station
In order not to store wrong parts – sets, the order is subjected to quality control. For this purpose, the mobile robot moves under a shaft in which an industrial camera is located. If unwanted parts are detected, the mobile robot moves to the bad parts storage to remove them.
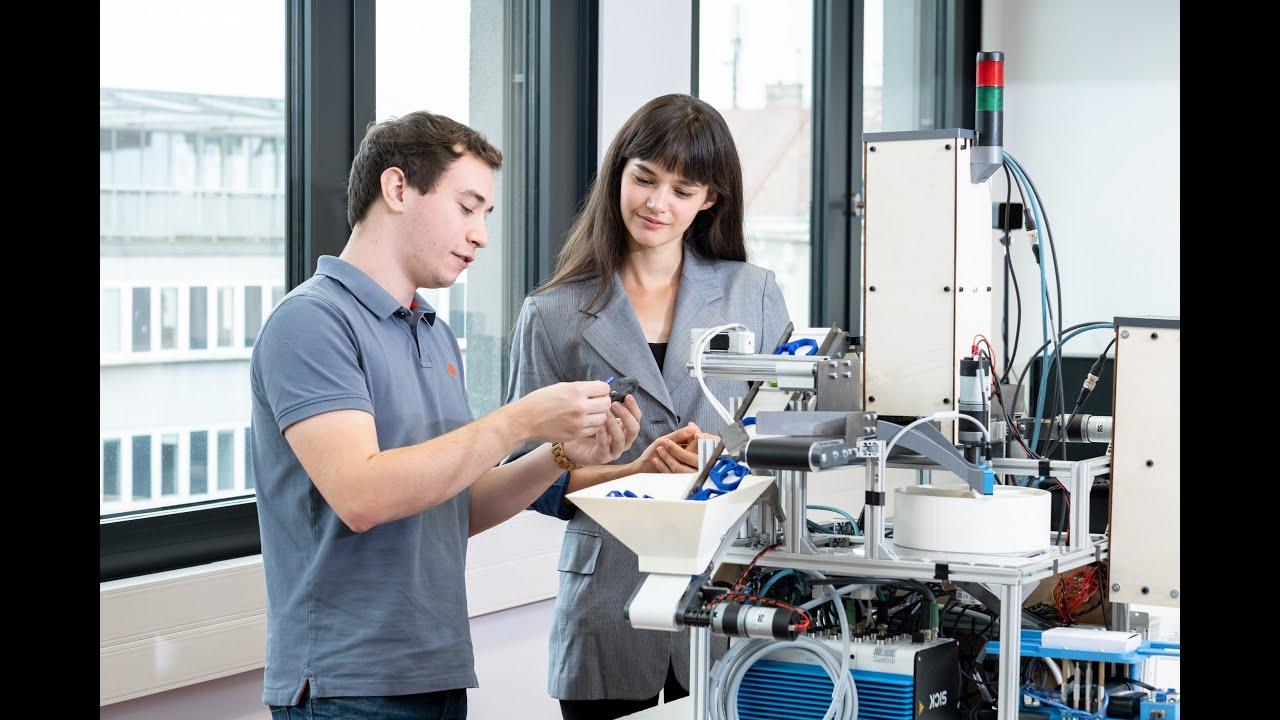
Please accept cookies for external media to view videos
Bad parts station
The faulty kit configurations detected during quality control are stored in the bad parts storage. For this purpose, the kit is removed from the mobile robot by means of a SCARA robot and stored in a stack.

Please accept cookies for external media to view videos
Contact
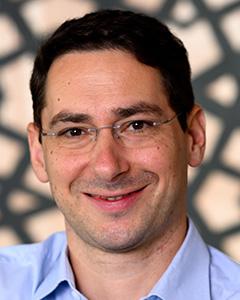
Head of Competence Center Industrial Product Life Cycle Technologies
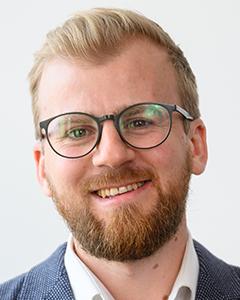
Lecturer/Researcher
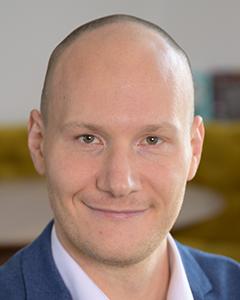
Lecturer/Researcher
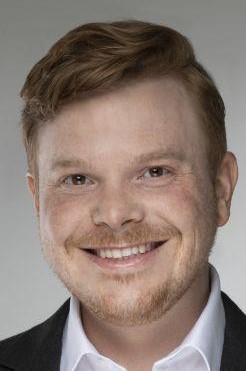
Lecturer/Researcher