High-Tech Paw for Dogs: UASTW Student Develops New Animal Prosthesis in Master’s Thesis
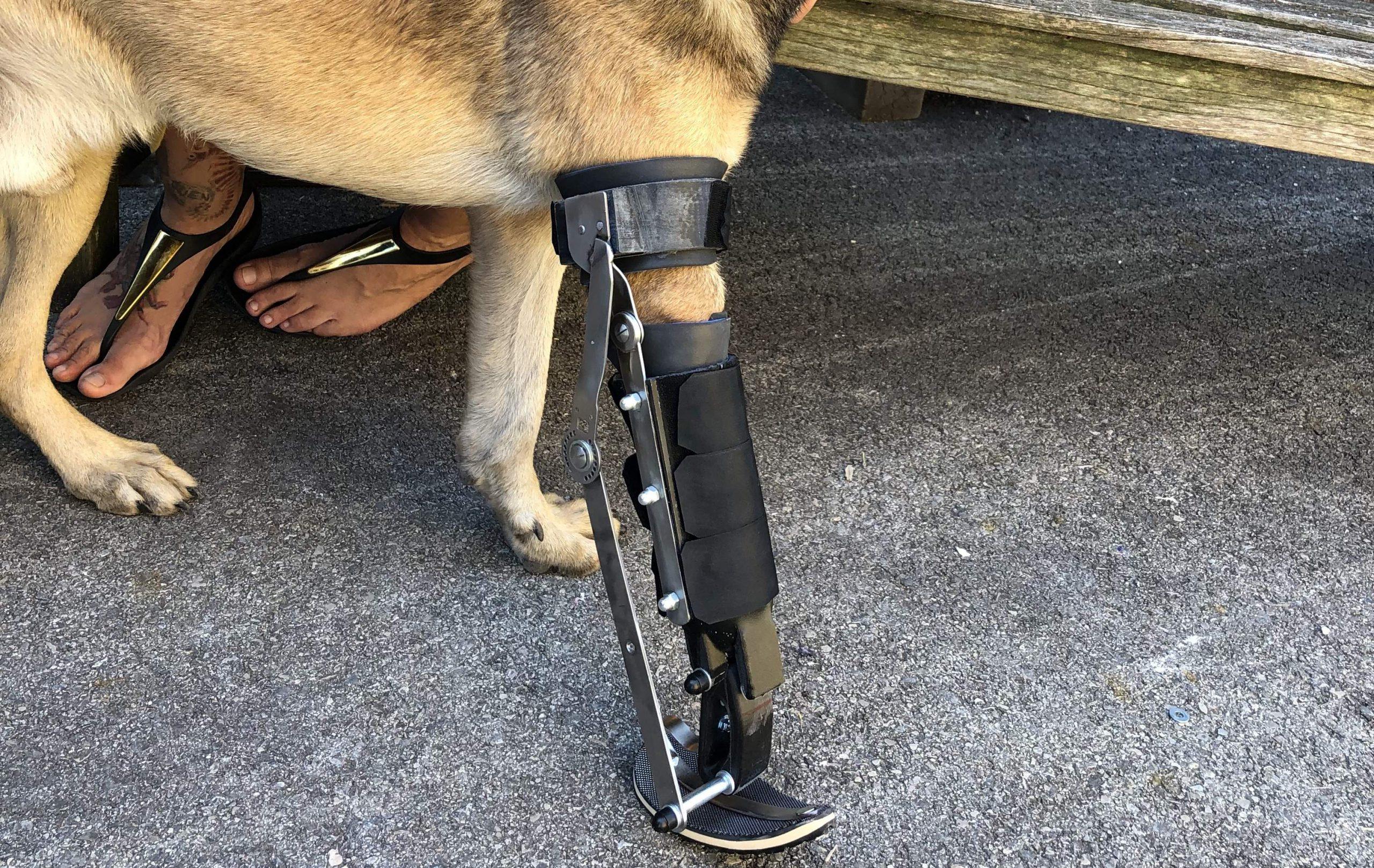
26 August, 2022
For his final thesis in the Master’s in Health and Rehabilitation Technology, Dominik Schneeberger is developing a self-powered prosthesis for dogs together with the University of Veterinary Medicine and the orthopaedic company Kerkoc: this is intended to enable animals that still have an intact elbow joint to move and posture more naturally.
Today, human prostheses are available in the most diverse, sometimes highly technological designs. There have also been prostheses for animals on the market for some years, but they are often simple, rod-like constructions. As part of his Master’s thesis in the Healthcare and Rehabilitation Technology program at the University of Applied Sciences Technikum Wien, Dominik Schneeberger is currently developing a prototype for a new type of canine prosthesis that is intended to enable better fitting of the lost limb based on natural movement.
Such functional intrinsic power prostheses have been used successfully in humans for some time. An important prerequisite for transferring the principle to dogs is that they have an intact elbow joint. This is where the movement of the prosthesis comes from, which in this way can replace the missing part of the leg like an artificial paw. “One problem in veterinary medicine is that often the whole limb up to the shoulder blade is removed. This also happens to reduce the risk of infection. A new prosthesis system could go some way to changing this practice,” Schneeberger says.
Relief for Healthy Limbs
The FFG-funded Master’s thesis is supervised at the Technikum by Junior Lecturer/Researcher Agnes Scheibenreif. Dominik Schneeberger is also working on his project with surgeon Eva Schnabl-Feichter from the University of Veterinary Medicine and the orthopaedic technology company Kerkoc.
Animals with amputated limbs often suffer from overloading of the healthy limbs due to uneven weight distribution. Prostheses not only support the animals in movement, but also provide relief by better distributing the body weight. For his first concept, Dominik Schneeberger developed a design in which the force is dissipated via the dog’s ribcage to protect the stump and prevent the formation of pressure points.
Complex Development Process
The development and construction of the 3D-printed prototypes is a complex process: plaster models of the ribcage and stump have to be created, which are then 3D-scanned so that the data can be further processed in the CAD program. In order to adapt the prototype to the dimensions of the dog, individual X-ray images must be taken for each animal. An orthopaedic analysis and a gait analysis without or with an existing prosthesis are also planned. Owners must also fill out questionnaires to assess their dogs’ functional limitations and pain.
During the tests of the first prototype, it turned out that the power transmission via the thorax does not work as well as planned in practice. The overall construction proved to be too large and clunky, and in addition, the dog frequently pulled the stump out of the prosthesis again. Schneeberger, who was able to use Kerkoc’s infrastructure for his experiments, therefore developed another concept in which the force transmission runs as gently as possible over the stump. “The new construction is much more delicate, we use stainless steel joints and 3D printing is only used where it is absolutely necessary.”
The final prototype has now been completed. In a further step, it still has to be analyzed in a test lasting several weeks how the dog copes with the prosthesis and how well the new system works compared to the old prosthesis. With the knowledge gained, Dominik Schneeberger hopes to be able to show that his artificial paw is a real improvement on the existing animal prostheses on the market.